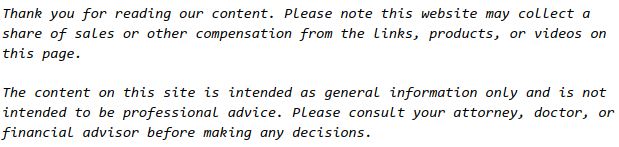

If an auto body shop doesn’t give enough attention to their compressed air piping layout, they will run into an improperly operating system. When running properly, a compressed air distribution system can cost less money than an improperly run one. There are three main problems that can cause a drop in air pressure, however when these problems are addressed the compressor piping may actually use up less energy overall. To see what your shop might be doing wrong and how to fix it, read below.
When Planning the Shop Layout, Don’t Forget About the Compressed Air Piping Layout.
Essentially, if your air fittings need to go around tight corners, or if you use a longer pipe fitting to reach across the shop floor, the chances of running into a problem increase dramatically. It all comes down to pressure efficiency. When pressure drops by more than 10% it could be a sign of one of the following problems.
moisture present when it’s compressed. Excessive moisture slows down air pressure in a compressed system, but adjustments to the temperature in the form of an air cooler can be helpful.
How to Save a Little on Those Utility Bills.
Properly working shop equipment does more than last longer than equipment that is poorly maintained. By running efficiently, it can actually require less energy when running. For example, a compressed air piping layout that has no sharp angles, obstructions, or excess moisture, might still have leaks. Leaks of as little as one eighth of an inch in a 100 psi system could cost the average shop about $1,200 over the course of a year in wasted energy. If all of these possible pitfalls are addressed, operating costs can be reduced 1.5% for every two pounds per-square-inch decrease in the compressor’s pressure.
One of the easiest ways to reduce costs in an auto body shop is to check your shop equipment and make sure it is running properly. For the air compressor system, this means checking for sharp angles, moisture, blockages, and leaks. If you witness a drop in pressure of more than 10% on the machine’s gauge, it’s time to do some checks.